喷雾流化床造粒机的工艺原理基于流态化技术与雾化喷涂的协同作用,通过动态流化、液滴包覆和连续干燥实现颗粒成型。其核心流程及机制如下:
一、工艺阶段与机制
1、流化阶段
预热后的空气从设备底部通入流化床,通过分布板形成均匀气流,使固体粉末悬浮并呈现流化状态。流化气体速度需高于颗粒的临界流化速度,以维持颗粒剧烈运动并防止结块。
2、雾化与喷涂
料液(如母液或黏合剂)通过压力泵输送至雾化喷嘴,被压缩空气或机械作用分散为微米级液滴。液滴通过以下方式与流化颗粒结合:
浸润与黏合:液滴润湿颗粒表面,形成液桥并黏附细粉;
凝集与包覆:部分液滴直接包裹颗粒或凝集细粉形成新颗粒核。
3、动态干燥与颗粒生长
液滴附着后迅速被热空气干燥,液桥转化为固体桥,颗粒通过反复喷涂和干燥逐步增大。干燥过程中,热空气与颗粒逆流接触,确保水分均匀蒸发并减少局部过热风险。
4、细粉回收与循环
未附着的细粉随气流进入旋风分离器或布袋捕集器,回收后重新引入流化床参与造粒,维持颗粒数量平衡并提升原料利用率。
二、工艺特点
1、一体化操作:整合混合、制粒、干燥流程,缩短生产周期;
2、热敏性适用:流化床内温度分布均匀,避免物料热分解;
3、颗粒质量高:颗粒圆整度好、粒径分布窄,流动性及压缩性优异;
4、密闭式生产:符合GMP规范,减少污染与人员接触风险。
三、关键控制参数
1、流化气体速度:影响颗粒混合效率与流化稳定性;
2、雾化压力/喷嘴类型:决定液滴粒径及喷涂均匀性;
3、料液黏度与温度:影响液桥形成强度与干燥速率;
4、热空气温度与流量:控制干燥速度及颗粒孔隙率。
四、应用场景
适用于制药、食品、化工等行业,尤其适合热敏性物料(如酶制剂、维生素)和需高均匀度颗粒的造粒需求。
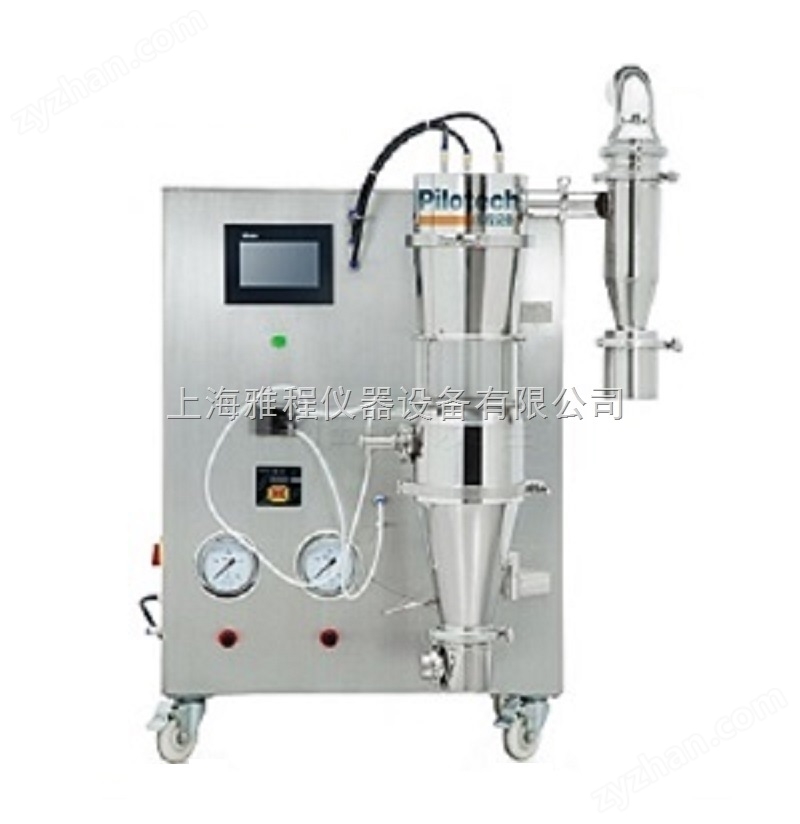